За одну поездку в г.Орел мы побывали на 2 заводах: по сантехнике и по плитке. В этой статье будет все только про завод плитки. Начнем:)
В 15:00 мы приехали с завода сантехники, на завод плитки. В столовой нас плотно накормили обедом из трех блюд (салат, суп, горячее и булочка с кофе)
В 15:00 мы приехали с завода сантехники, на завод плитки. В столовой нас плотно накормили обедом из трех блюд (салат, суп, горячее и булочка с кофе)
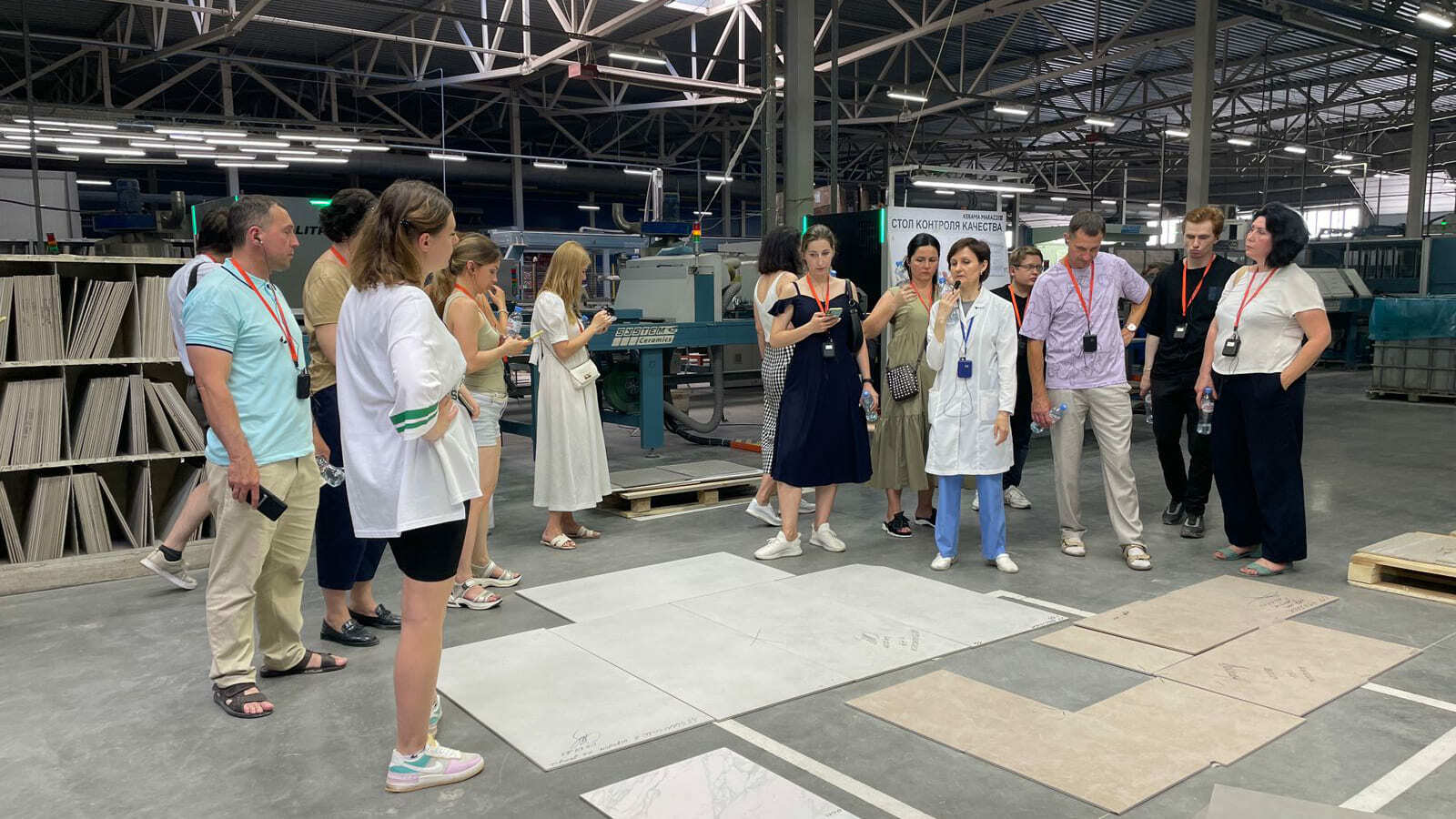
Завод огромен! в 2022 году завод Kerama Marazzi выпустил 40,5 милн. кв. метров керамической плитки
Статистика поражает)
Вся экскурсия у нас заняла 4 часа. Надеюсь, на прочтение статьи у тебя, мой читатель, уйдет намного меньше времени. Читай дальше, сможешь увидеть этот масштаб моими глазами.
Статистика поражает)
Вся экскурсия у нас заняла 4 часа. Надеюсь, на прочтение статьи у тебя, мой читатель, уйдет намного меньше времени. Читай дальше, сможешь увидеть этот масштаб моими глазами.
Какую продукцию выпускает завод?
- керамическую плитку для стен
- напольную плитку
- керамогранит
- мозаику
- столешницы
- ступени
Весь завод разбит на 4 вида производства:
БИКО - (сокр. от бикоттура, с итал. "двойной обжиг") самое объемное производство, здесь выпускается керамическая плитка для стен
МОНО - (сокр. от монокоттура, с итал. "одинарный обжиг") здесь выпускается напольная керамическая плитка
ГРЕС - здесь изготавливают керамогранит
Производство третьего обжига, специальных декоративных изделий и мозаики - название говорит за себя, здесь выпускают мозайку, столешницы, ступени и другие эксклюзивные элементы декора
Как делают плитку? Обзор с производства Kerama Marazzi
- отбирают сырье
- производят пресс-порошок
- производят сырцы
- обжигают
- глазируют
- наносят рисунок
- повторно обжигают
- сортируют
- упаковывают и отправляют заказчику
А теперь пойдем на производство смотреть каждый этап
Отбор сырья
Для создания пресс-порошка нужны: глина, шпат, песок, мел и шамот. Все ингредиенты доставляются на склад больших мешках, а потом пересыпаются в резервуары.
Шамот - это переработанная бракованная плитка. Как говорят сотрудники с улыбкой "без плитки не сделать плитку) но и мы стремимся к безотходному производству"
Шамот - это переработанная бракованная плитка. Как говорят сотрудники с улыбкой "без плитки не сделать плитку) но и мы стремимся к безотходному производству"
Производство работает круглосуточно, каждый день сотрудники получают технологическую карту в соответствии с которой начинают делать новые партии. В соответствии с технологической картой сырье перемешивают и отправляют в другой цех
Производство пресс-порошка
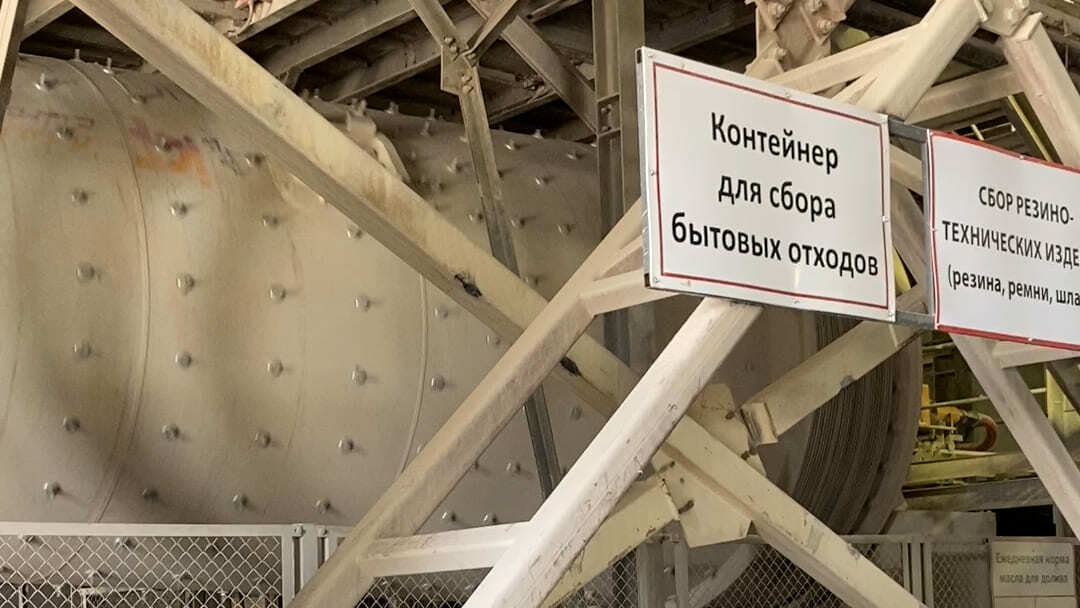
На фото мельница непрерывного помола. Напротив нее располагается еще мельница периодического помола, ее включают по необходимости.
В мельницу добавляют воду и гальку. Интересно, что гальку добывают на проливе Ла-Манш, говорят она идеально подходит по химическому составу для создания пресс-порошка
В мельницу добавляют воду и гальку. Интересно, что гальку добывают на проливе Ла-Манш, говорят она идеально подходит по химическому составу для создания пресс-порошка
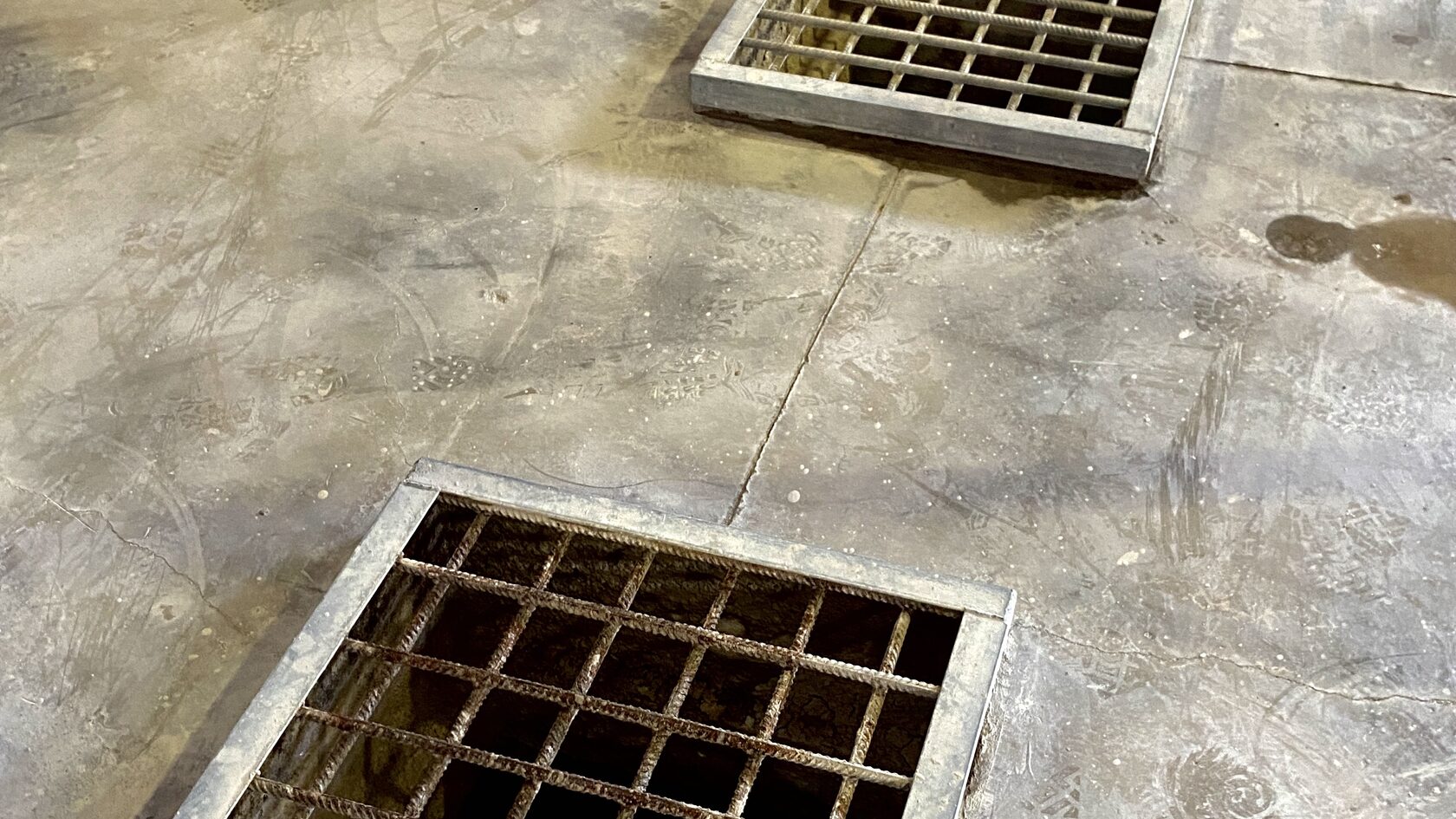
Все ингредиенты измельчаются и перемешиваются с водой до жидкой массы, которую называют шликер. Он перетекает в огромные подземные резервуары, они на фото
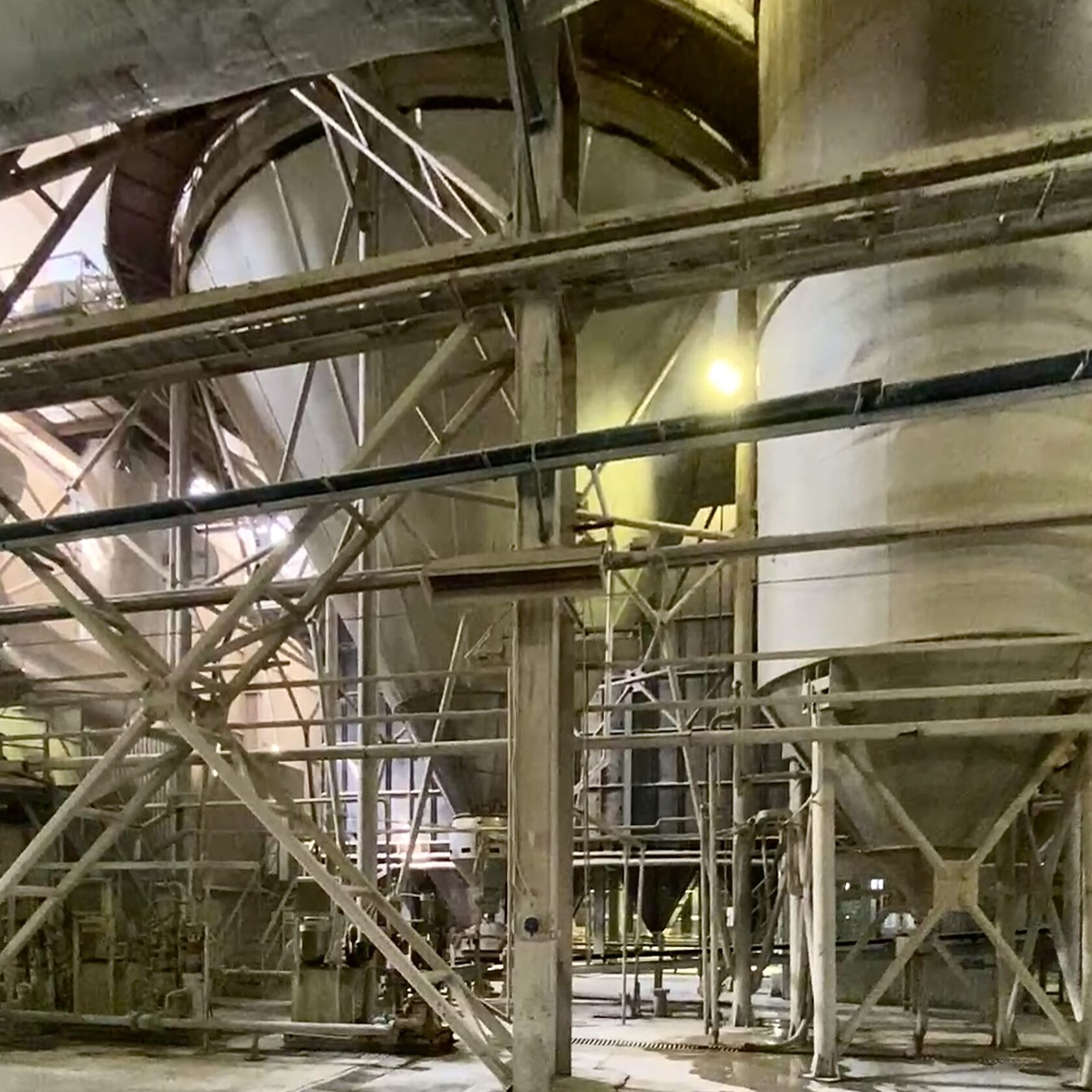
Шликер перекачиваются в эту большую воронку. Температура в ней около 500 градусов. Под температурой выпаривается вода и остаётся только порошок, из которого и делают плитку
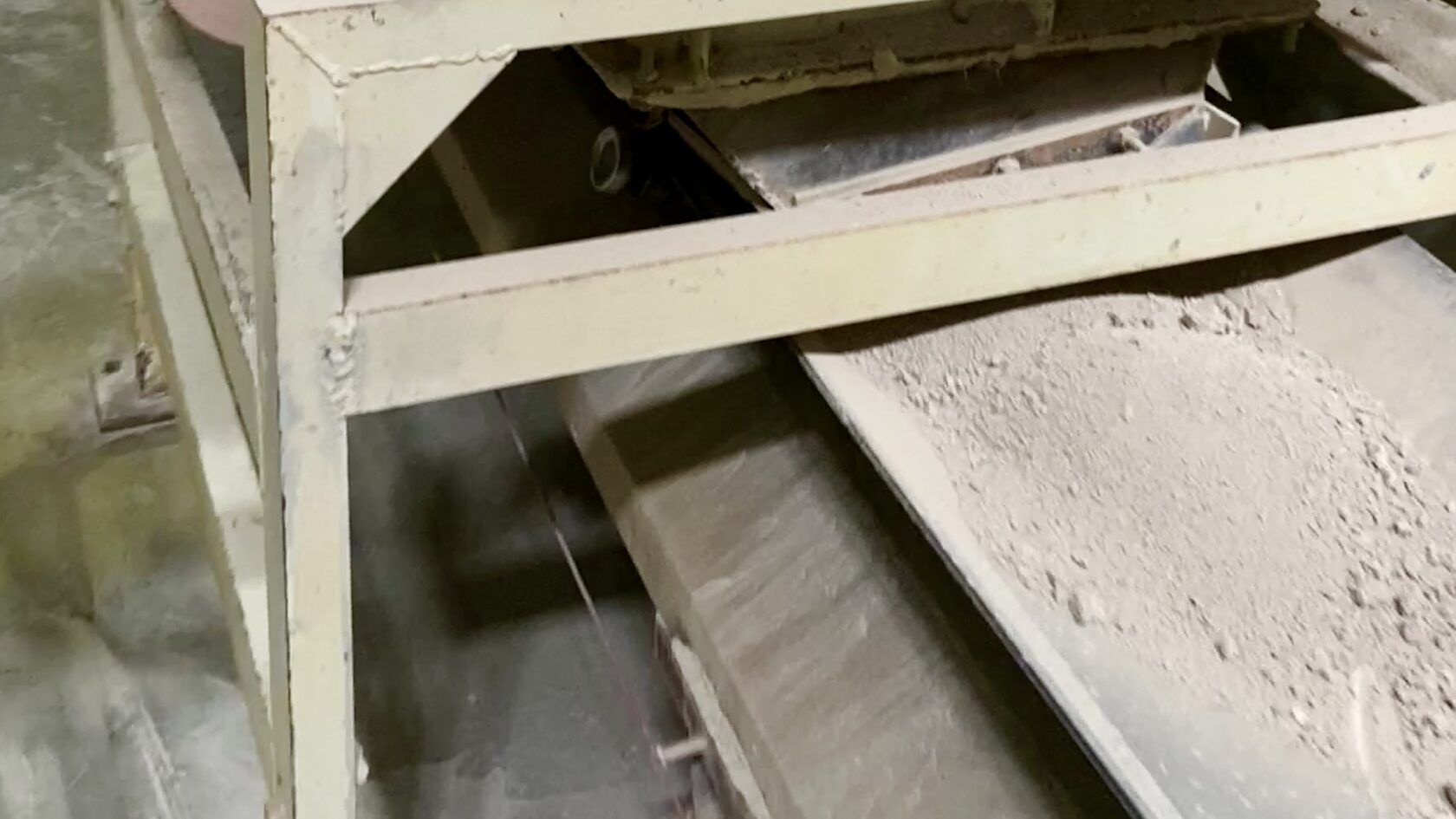
По конвейеру пресс-порошок отправляется в места хранения
Производство сырцов
Здесь изготавливают необожженную плитку - сырцы. Здесь создается оборотная сторона плитки, кстати, на каждой плитке делают маркировку. Дальше на конвейерной ленте плитка перевернется лицевой стороной и поступит на следующий этап, где ее ждет первый обжиг
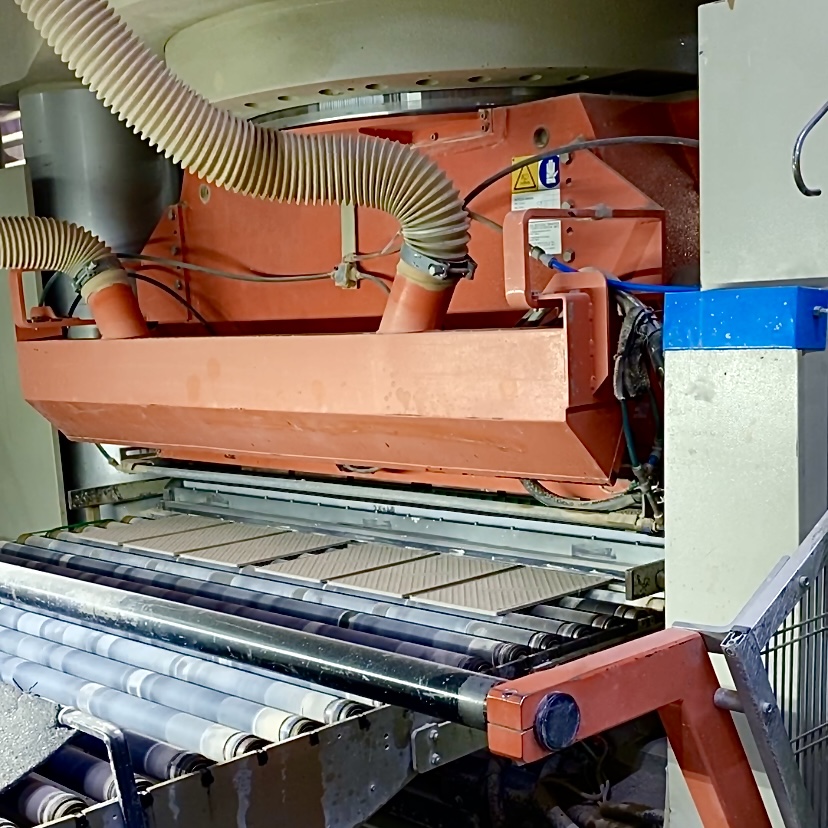
Обжиг
В сырцах очень много влаги, поэтому они легко могут сломаться. Первый обжиг делает их более прочными. Но как сказала экскурсовод "чтобы не подгорели" сырцы покрывают специальным составом.
Несколько фактов о первом обжиге
Несколько фактов о первом обжиге
- печь двухъярусная
- длина печи 119 метров
- цикл обжига 34 минуты
- плитка после обжига уменьшается в размерах примерно на 2 см с каждой стороны
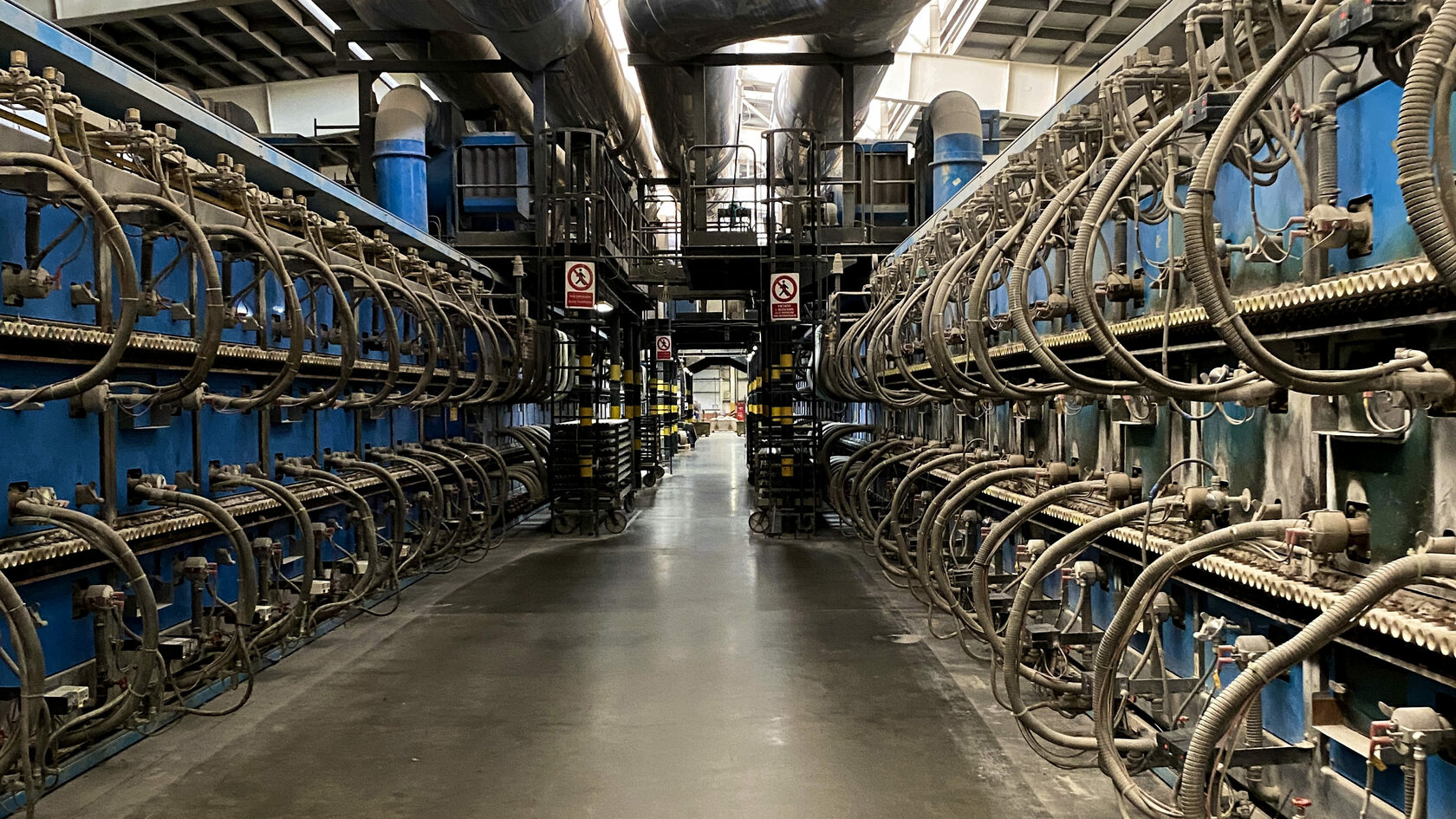
После обжига будущая плитка разгружается на каретки, а потом робот перевозит заполненную каретку в зону временного хранения, где плитка остывает.
Глазурование
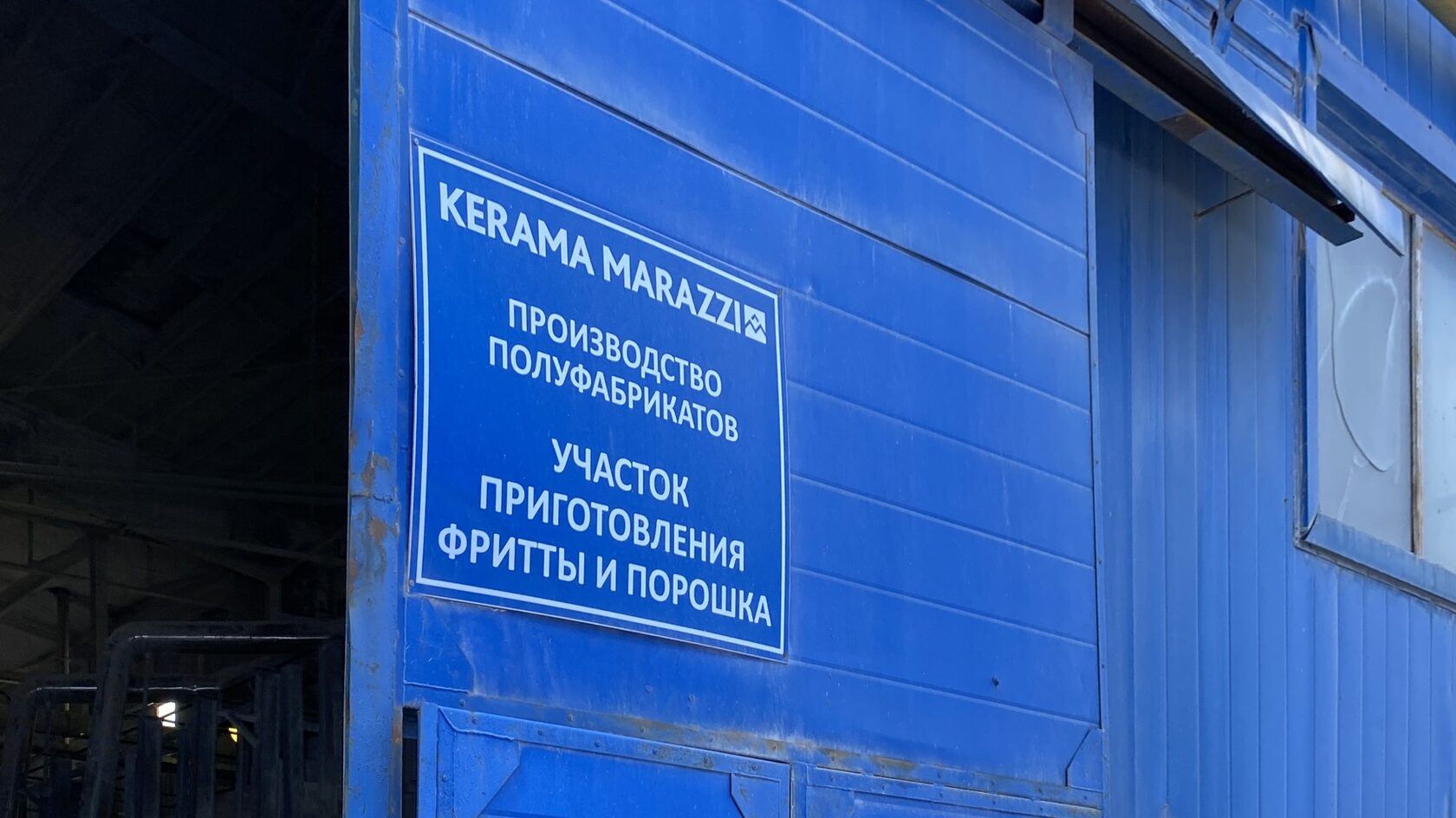
Для дальнейшего производства нужна глазурь, которой покрывают плитку. Заходим на участок фритты
Основной ингредиент глазури - фритта, остальная часть - добавки.
фритта - гранулированное стекло, 75-90%
Основной ингредиент глазури - фритта, остальная часть - добавки.
фритта - гранулированное стекло, 75-90%
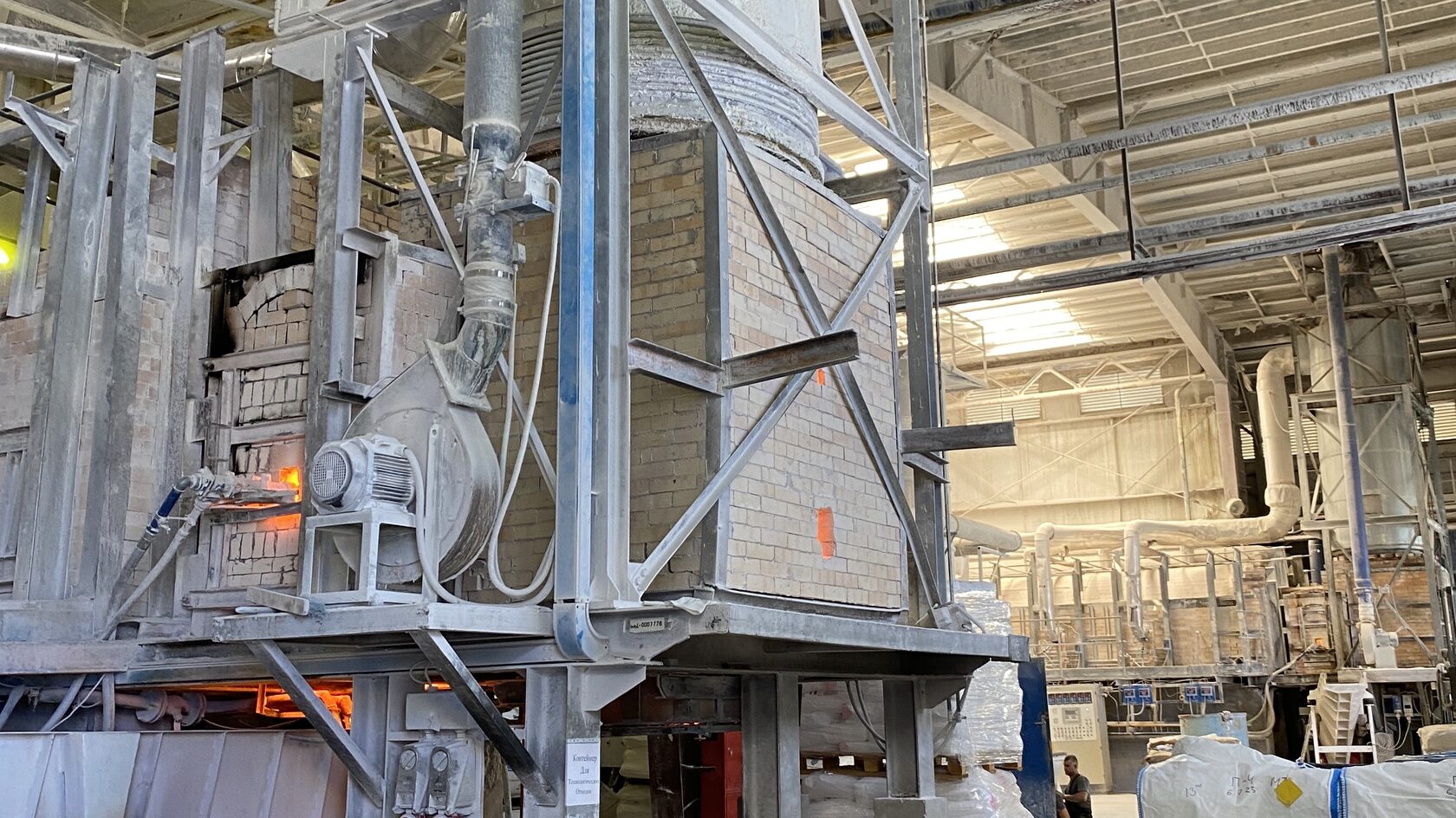
На фото фриттоварочная печь
На входе добавляются все основные компоненты, выставляется температура 1500 градусов, варится фритта.
Затем она попадает в воду температурой 38 градусов, где остывает и приобретает форму
На входе добавляются все основные компоненты, выставляется температура 1500 градусов, варится фритта.
Затем она попадает в воду температурой 38 градусов, где остывает и приобретает форму
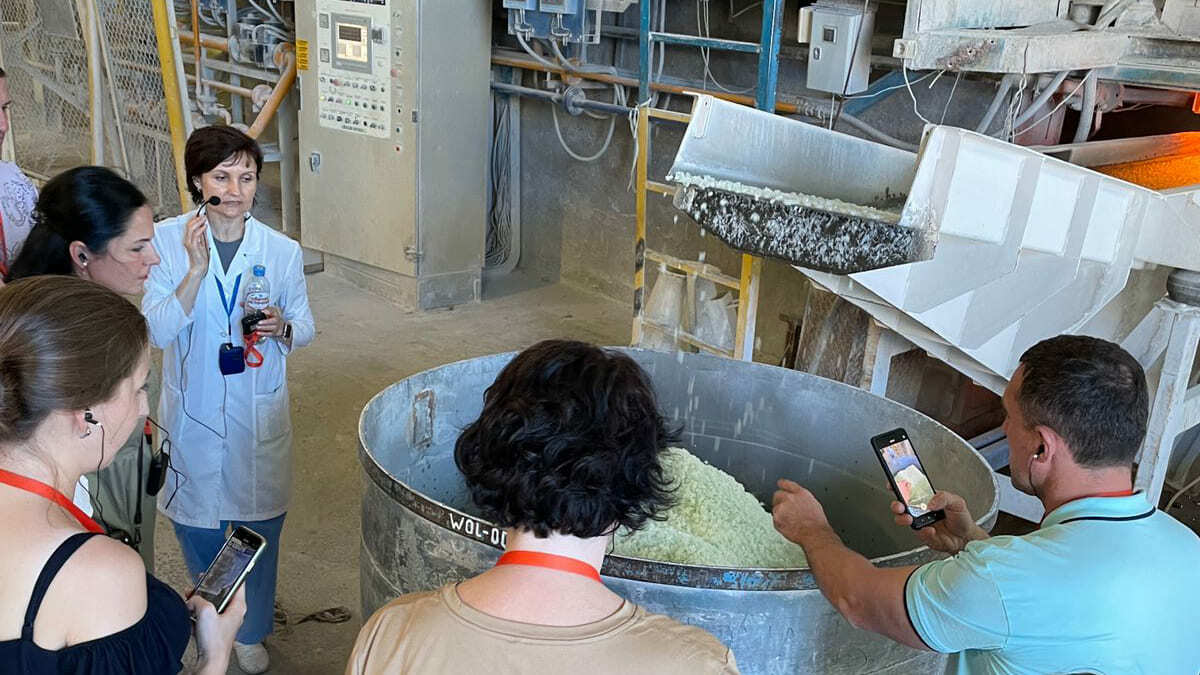
На фото готовая фритта падает в резервуар
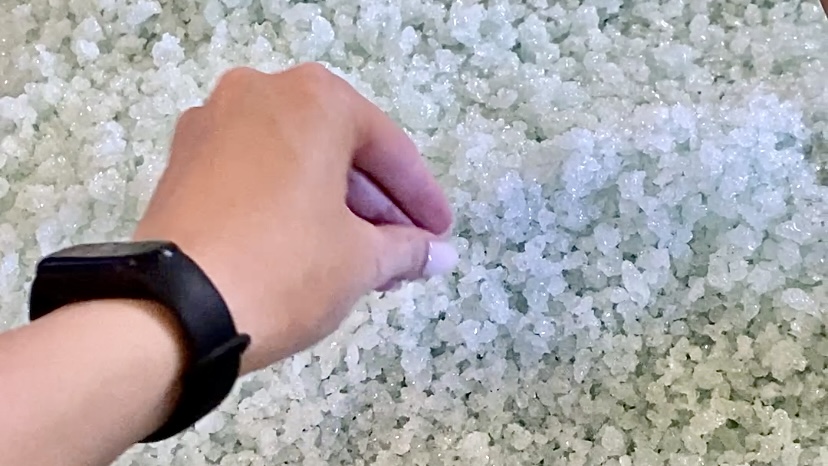
Нам разрешили потрогать:) на ощупь теплая стеклянная крошка с мягкими углами
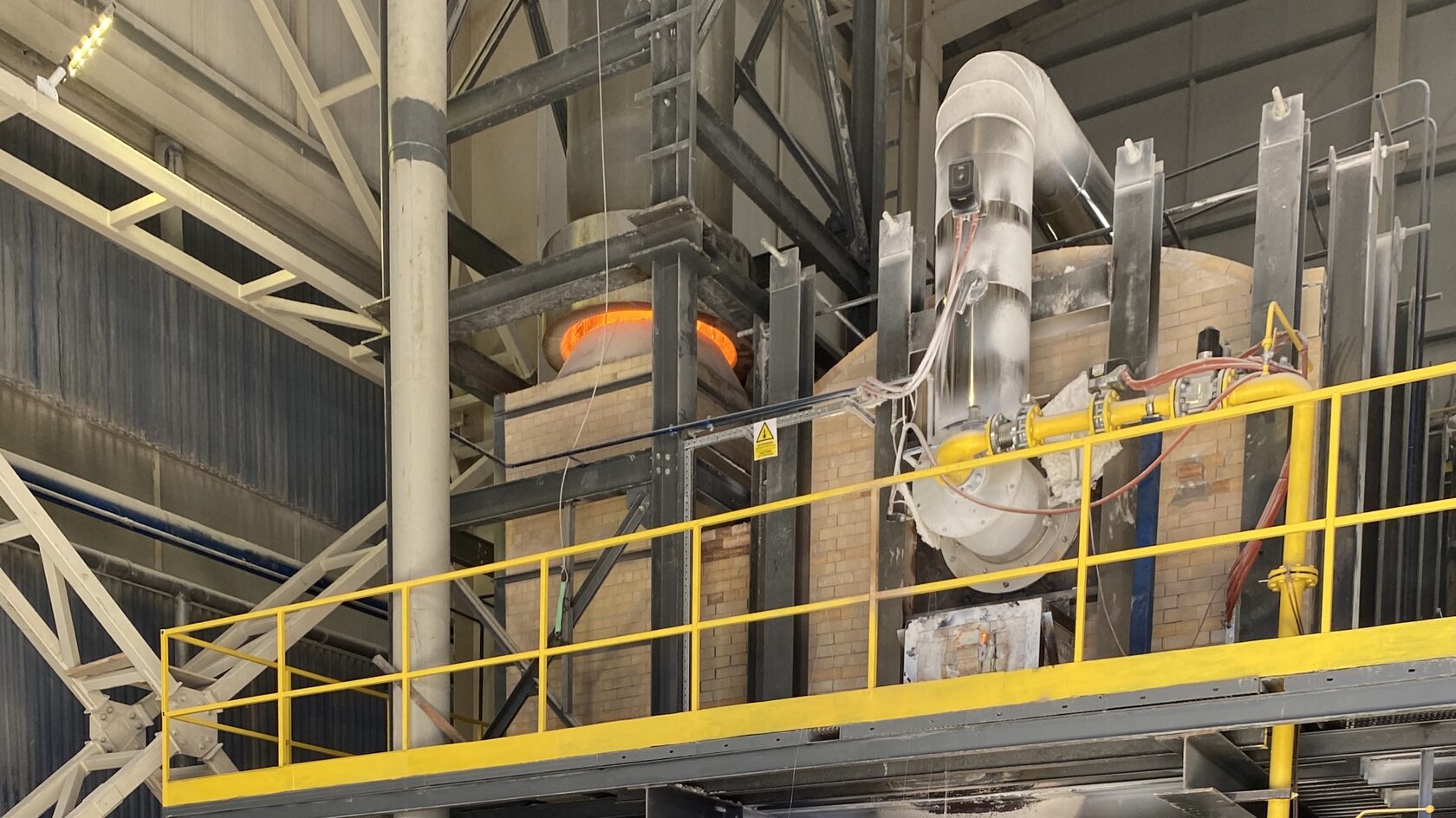
Производство расширяется. Первый участок фритты уже не справляется с варкой, на производстве недавно построили вторую печь
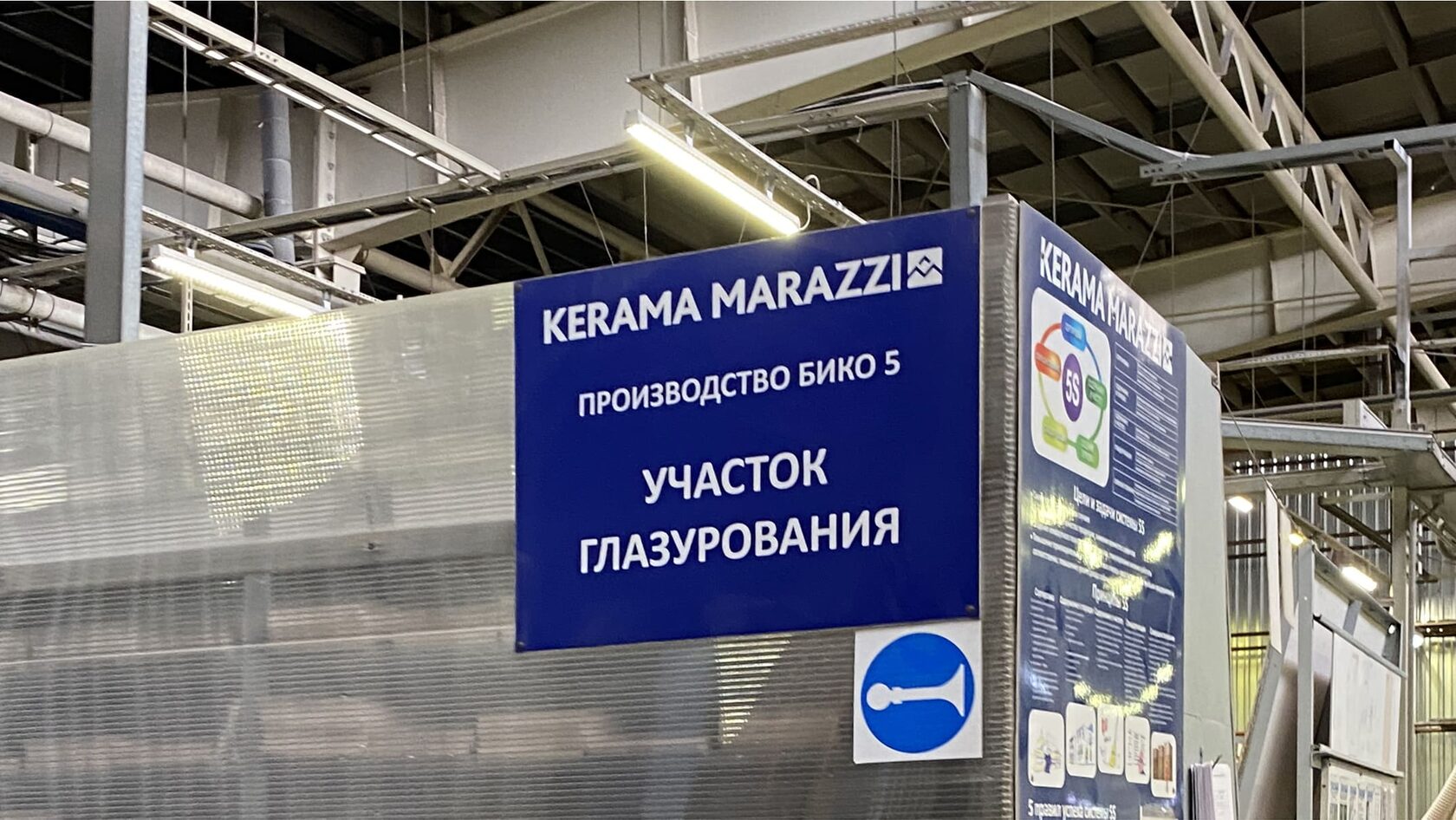
После первого обжига плитка покрывается глазурью. Рисунок наносится машиной, оператор тщательно контролирует весь процесс. Сначала зачищаются края, затем машина поливает каждую плитку глазурью, она становится идеально белой, снова зачищаются края.
Основа готова, наступает этап нанесения рисунка
Основа готова, наступает этап нанесения рисунка
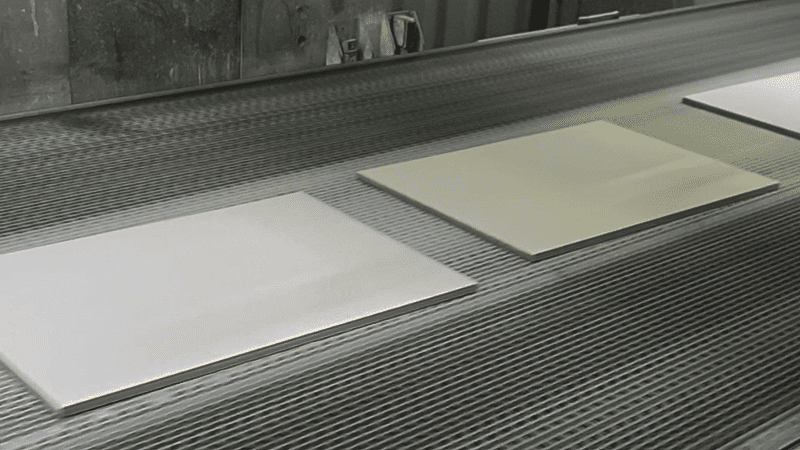
Нанесение рисунка
Есть несколько способов нанесения рисунка на плитку
На фото ниже цветовая машина. Для каждого артикула уже загружена своя графика. Но тем не менее партии одного артикула иногда отличаются. Но насколько будут отличатся партии можно сказать только после обжига.
- шелкография
- ротативная печать
- цифровая печать
На фото ниже цветовая машина. Для каждого артикула уже загружена своя графика. Но тем не менее партии одного артикула иногда отличаются. Но насколько будут отличатся партии можно сказать только после обжига.
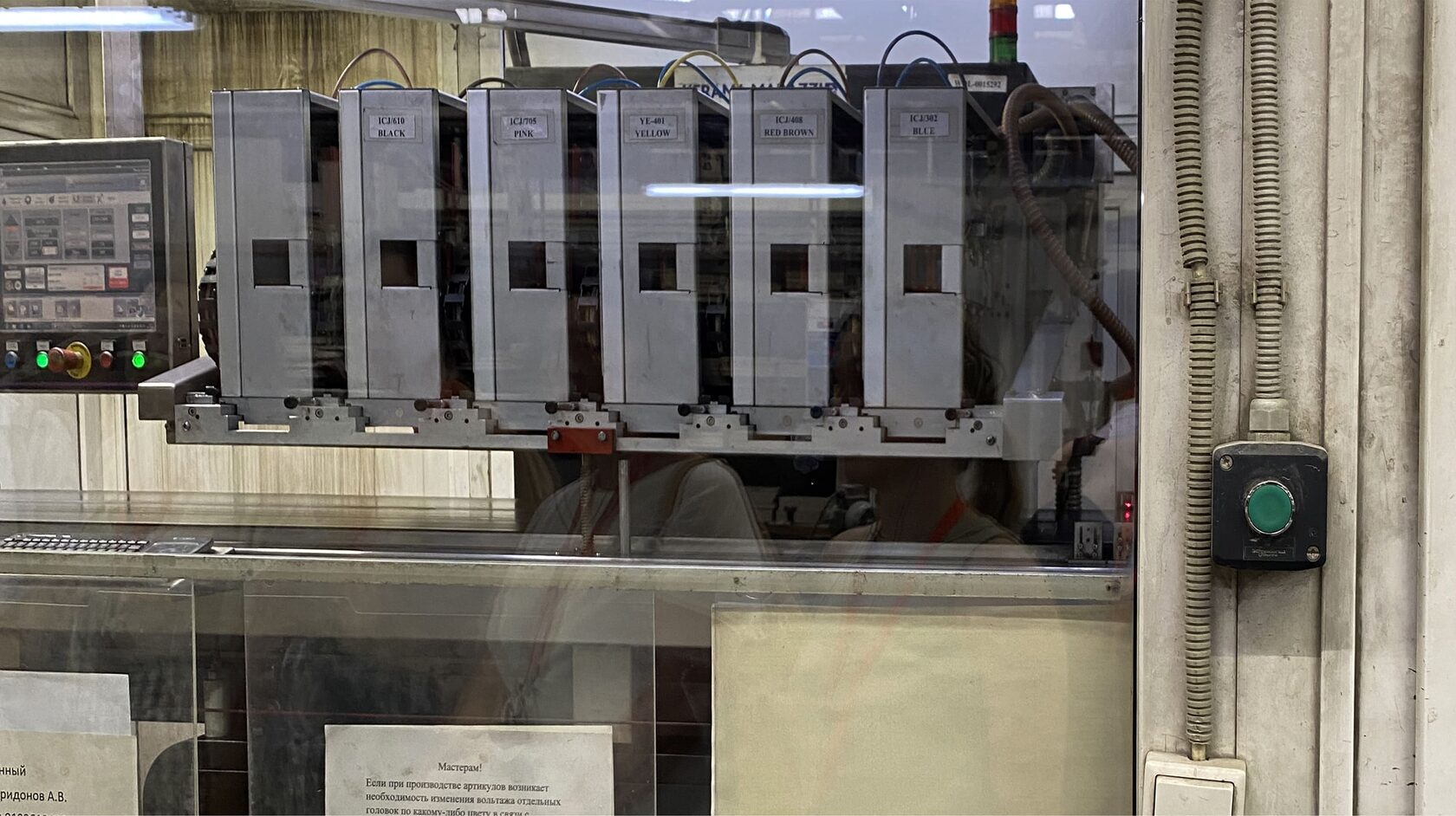
Второй обжиг
После второго обжига уже получают готовую продукцию, которая отправляется на сортировку и упаковку.
На фото ниже готовая плитка (под бетон, один из самых популярных артикулов сейчас) только из печи. она очень теплая на ощупь
На фото ниже готовая плитка (под бетон, один из самых популярных артикулов сейчас) только из печи. она очень теплая на ощупь
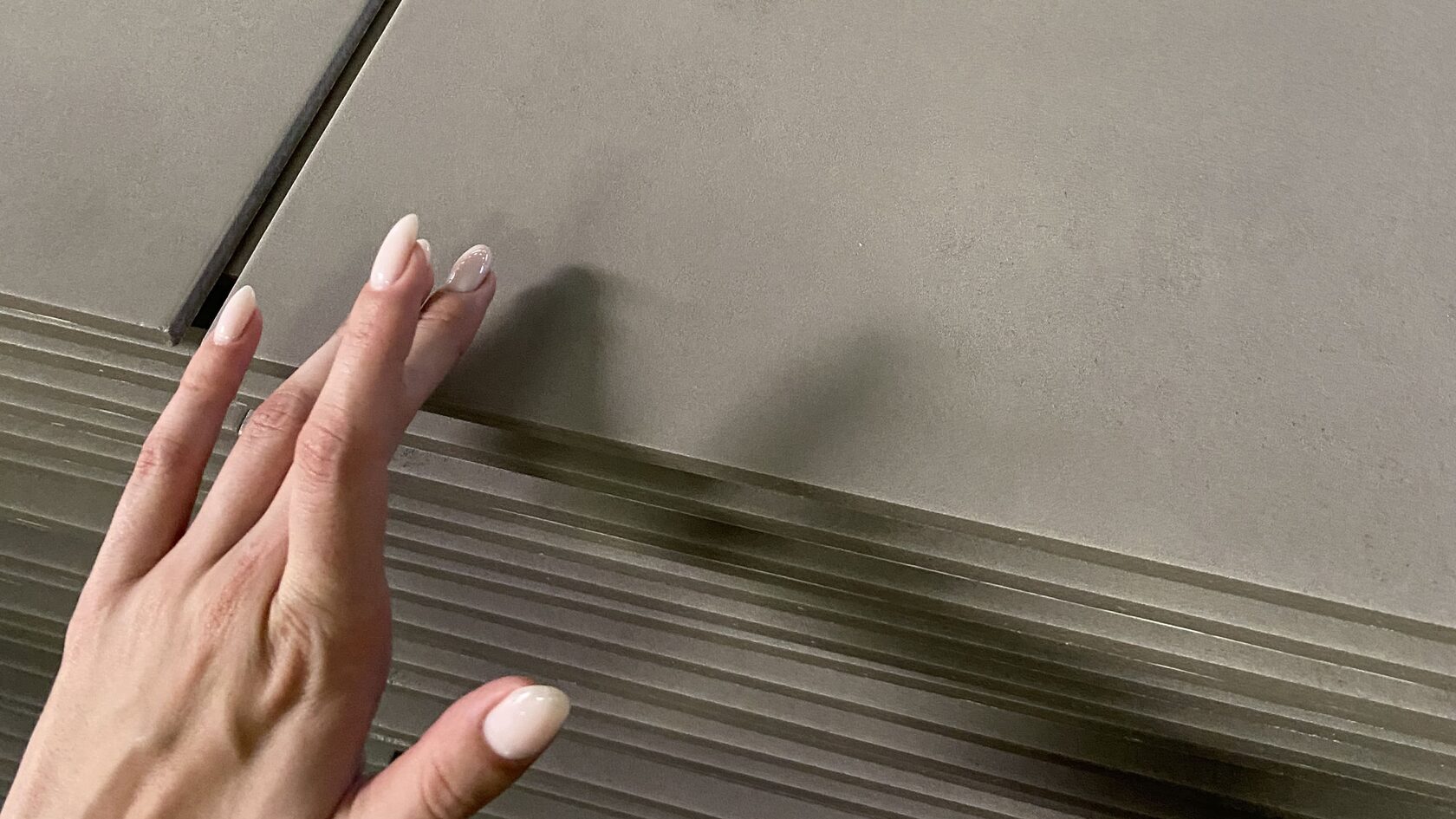
Сортировка
После обжига технолог сравнивает цвет с образцом и корректирует его в случае разницы.
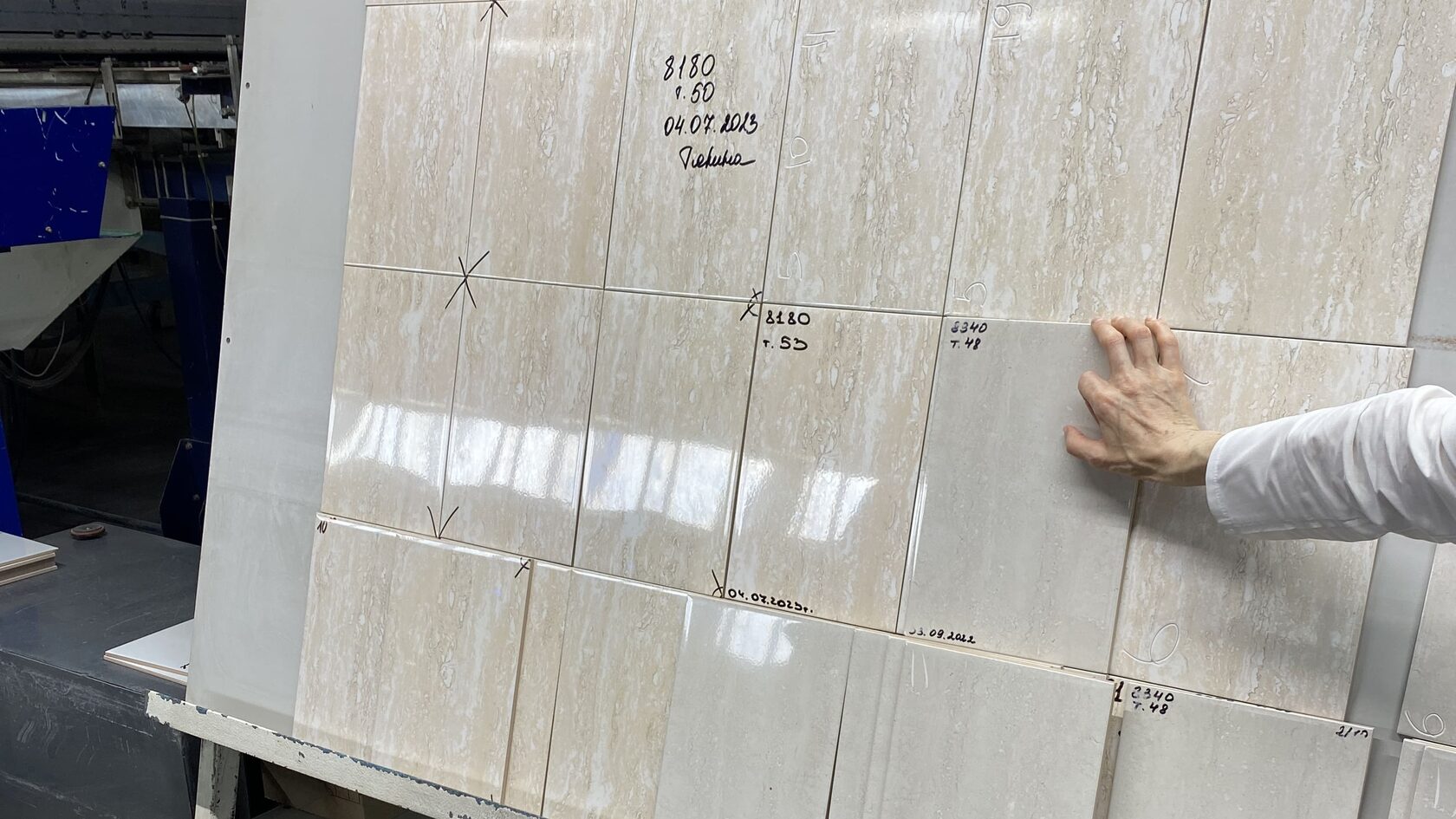
Линия сортировки очень тщательно проверяет всю продукцию на брак, проверяется кривизна плитки. Отбракованная продукция сразу же уходит с линии
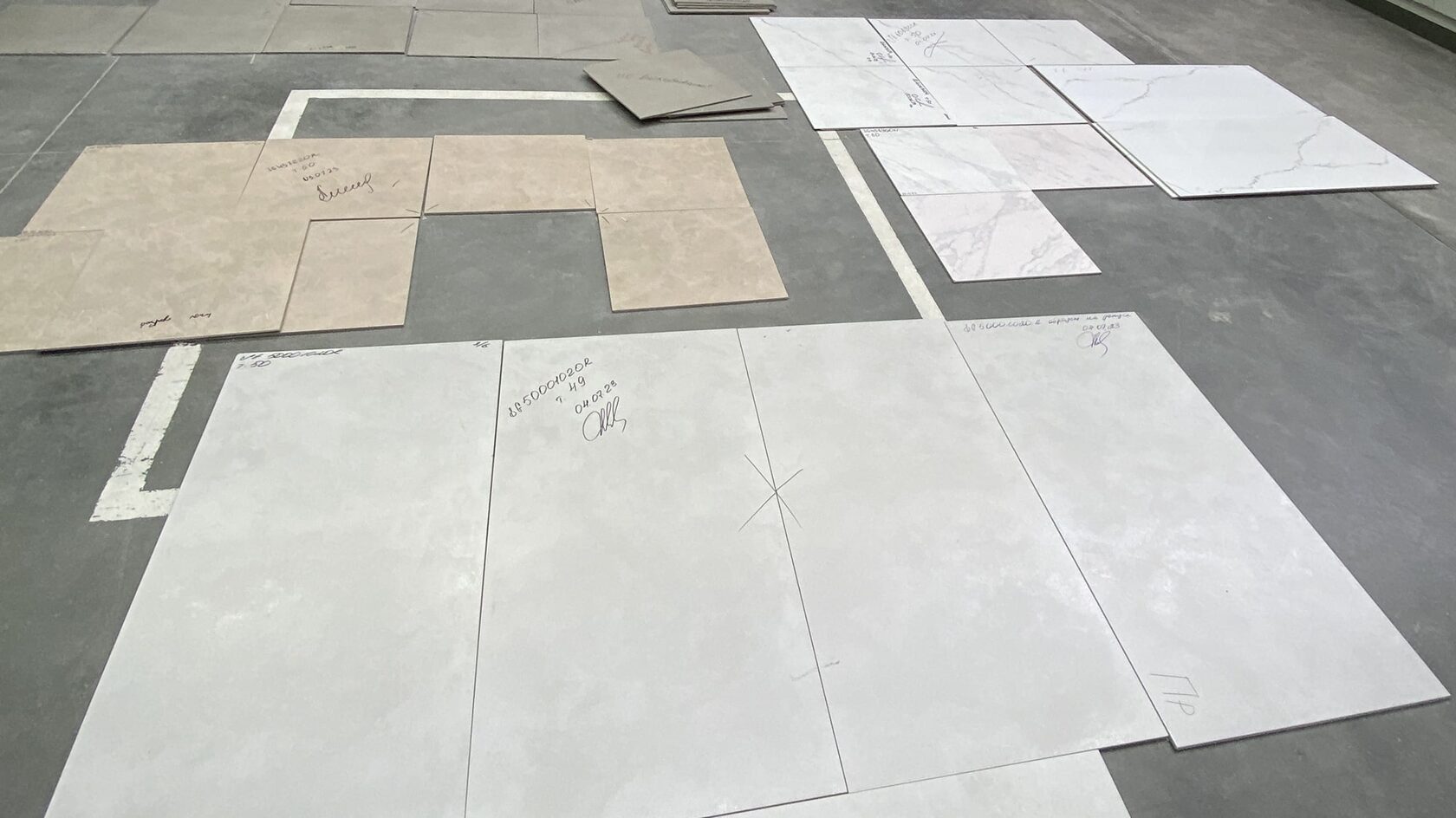
Упаковка
Самый последний этап
Здесь вся плитка будет упакована в коробки и отправится на склад, а оттуда к покупателям.
На каждой коробке автоматически проставляется артикул, тон и сорт плитки
Здесь вся плитка будет упакована в коробки и отправится на склад, а оттуда к покупателям.
На каждой коробке автоматически проставляется артикул, тон и сорт плитки
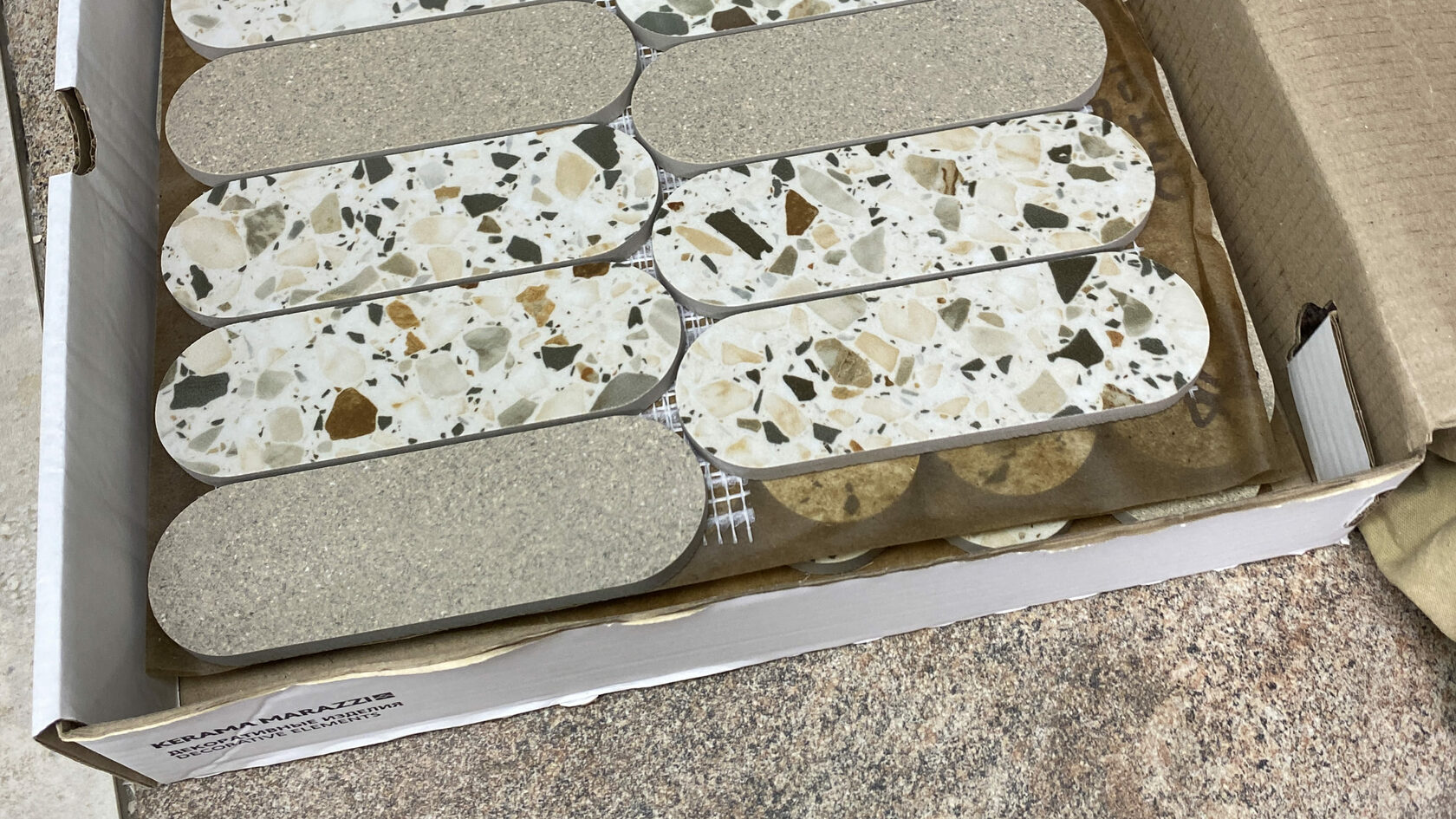
Производство сложных элементов: мозаика, ступени, столешницы
Производством всех сложных элементов занимается линия третьего обжига, которая существует уже 30 лет, а подсчет продукции ведется поштучно. Крупные изделия выпускают на автоматизированном производстве, а мозаику, элементы декора изготавливают с использованием ручного труда
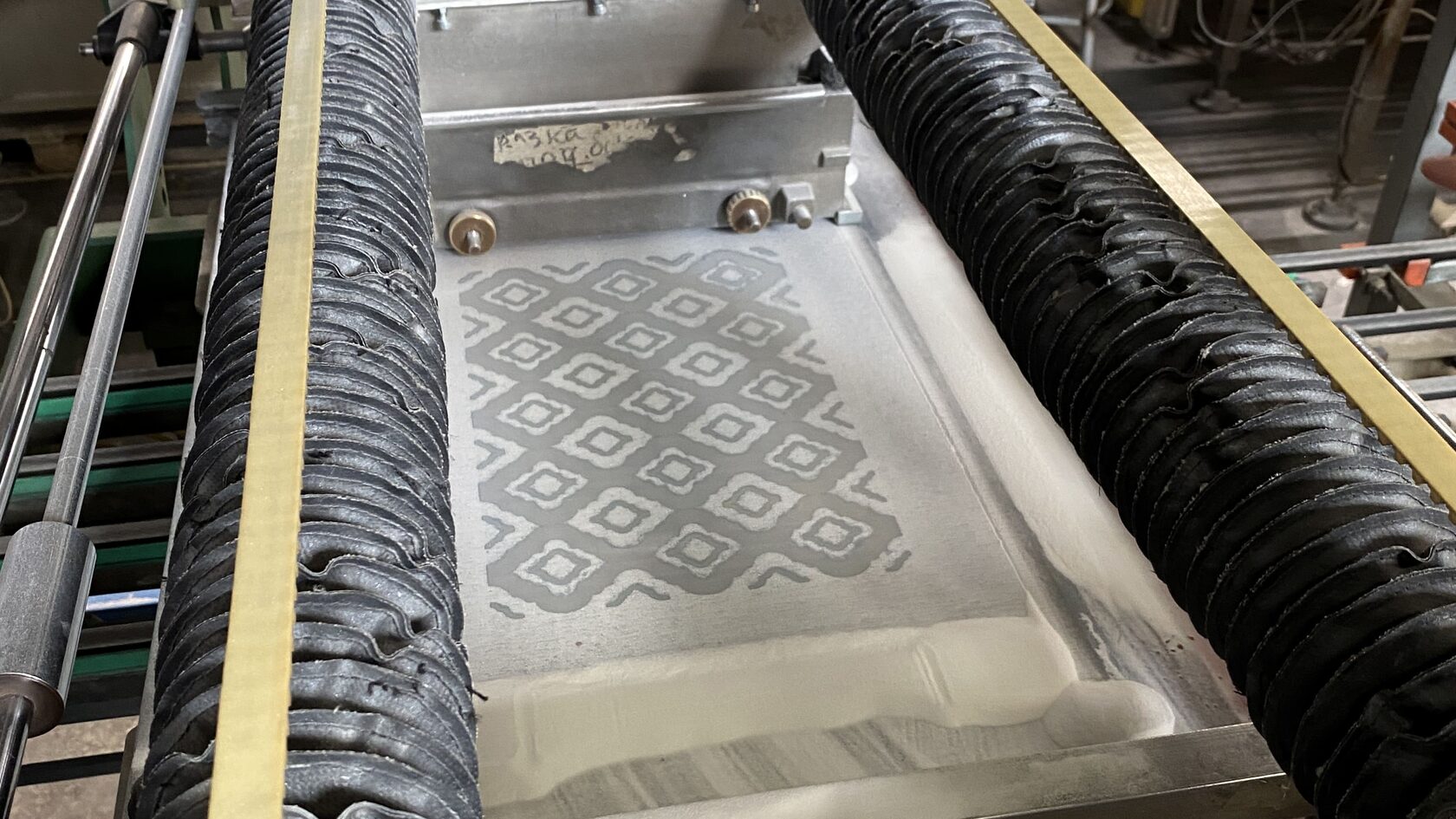
Здесь есть 2 вида нанесения рисунка - шелкография и цифровая печать. Процесс наненсения рисунка проходит в несколько этапов. Есть артикулы, которым требуется 9 машин для нанесения полного рисунка.
Отдельное место на этой линии занимают планшеты - образцы каждого артикула
Отдельное место на этой линии занимают планшеты - образцы каждого артикула
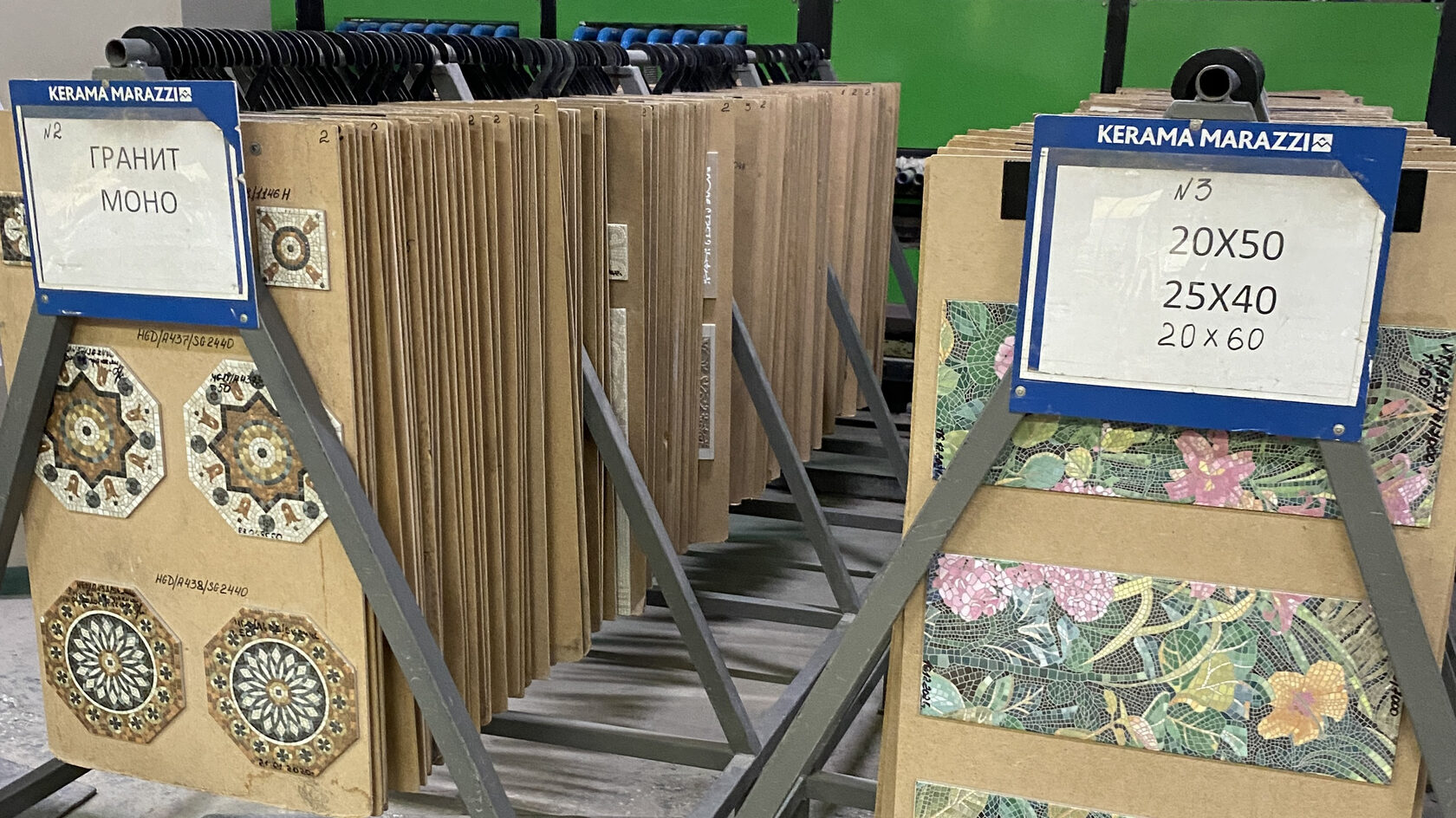
Линия мозаики
Здесь есть автоматическая и ручная сборка. Сложные элементы собирает мастер, приклеивает их на планшет, это очень кропотливая работа.
Здесь есть автоматическая и ручная сборка. Сложные элементы собирает мастер, приклеивает их на планшет, это очень кропотливая работа.
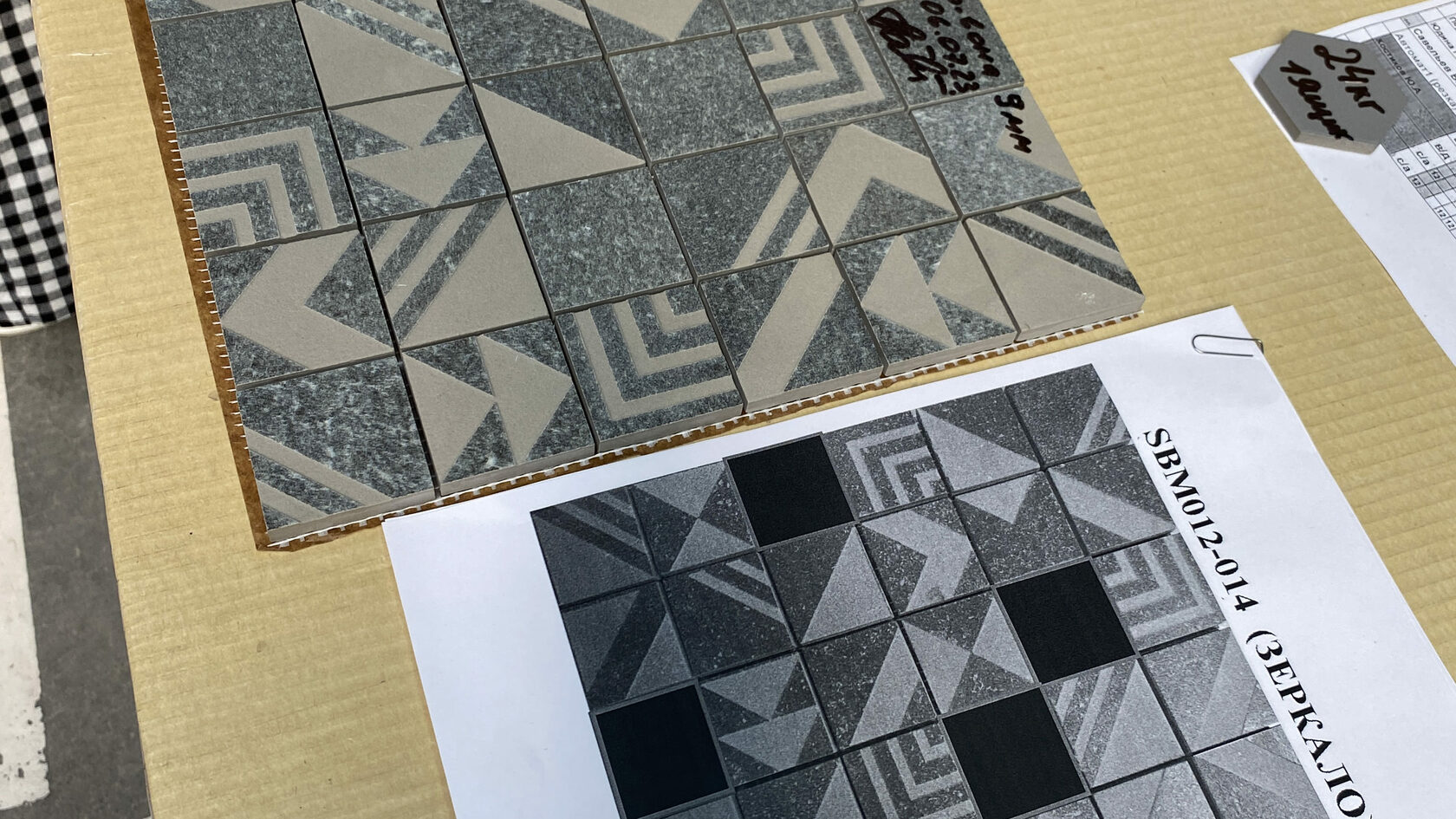
Участок фрезерованных ступеней
Ступени сборные, каждая состоит из 3х элементов
Удобное решение, мы в проектах использовали уже пару раз
Ступени сборные, каждая состоит из 3х элементов
Удобное решение, мы в проектах использовали уже пару раз
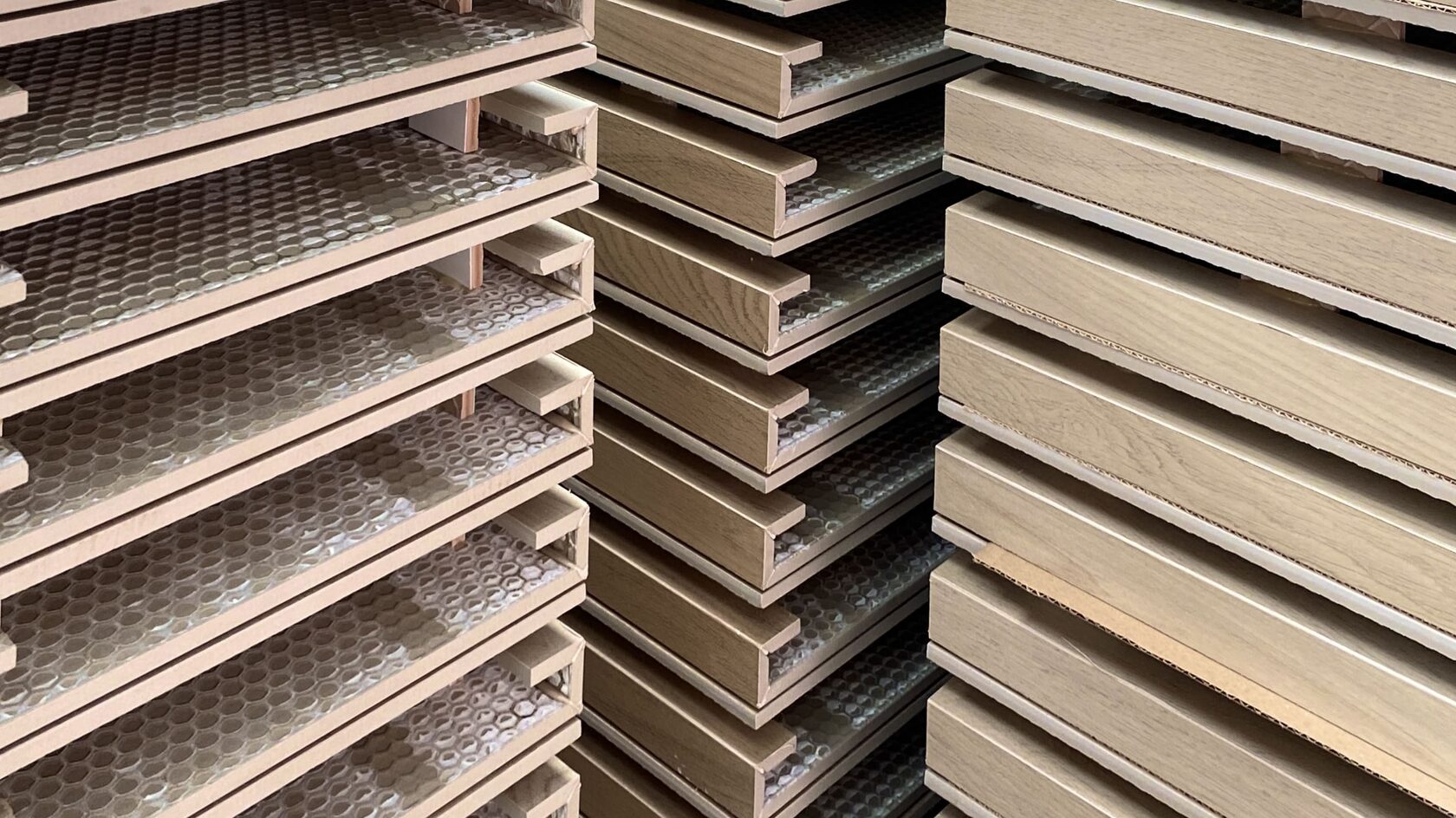
Участок производства столешниц.
Главное достоинство столешницы из керамогранита – долговечность и простота ухода, столешница гарантированно прослужит вам десятки лет. На производстве могут сделать практически любую столешницу под размеры проекта, но чаще это стандартные изделия
Главное достоинство столешницы из керамогранита – долговечность и простота ухода, столешница гарантированно прослужит вам десятки лет. На производстве могут сделать практически любую столешницу под размеры проекта, но чаще это стандартные изделия
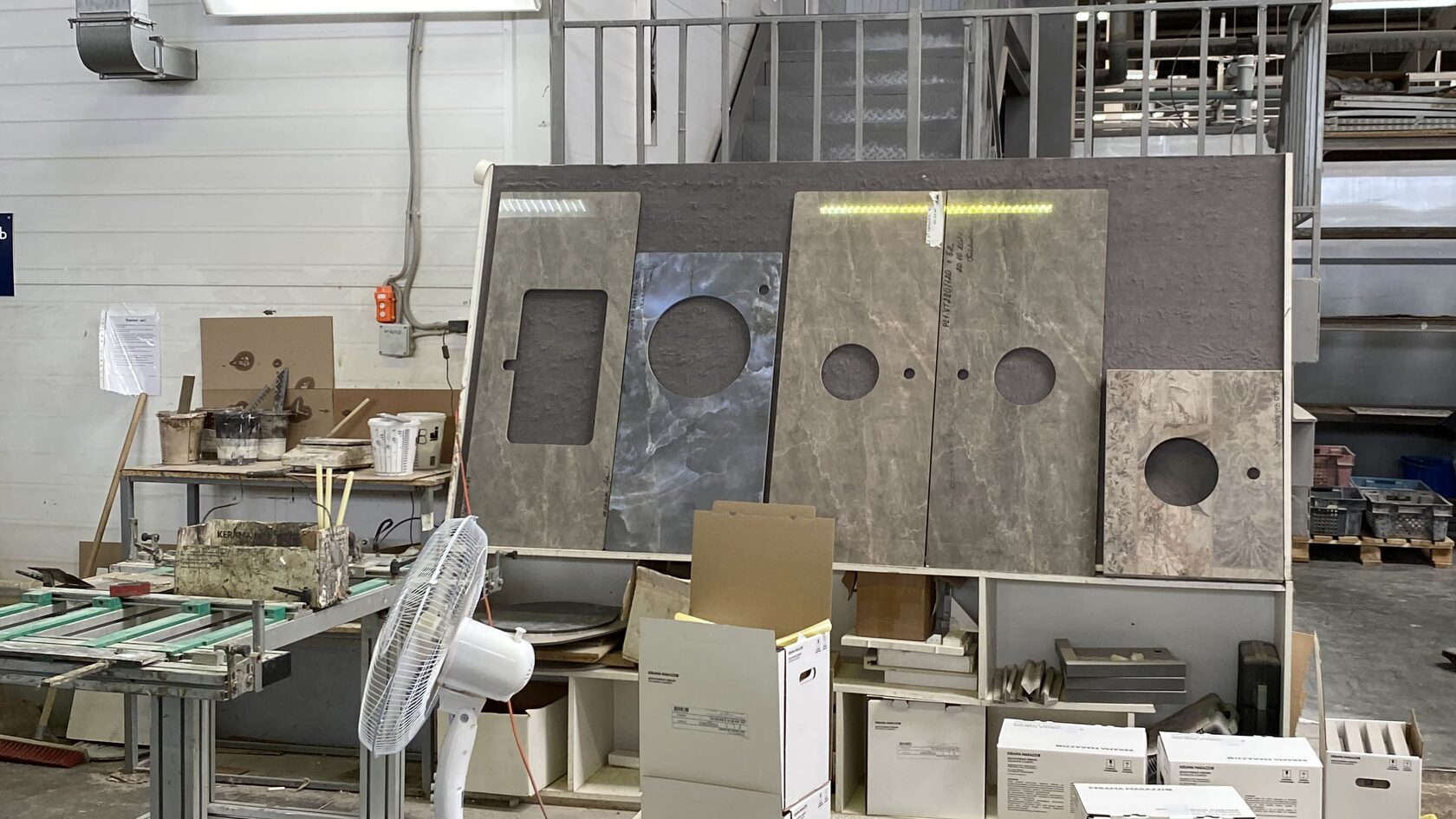
"На этом экскурсия по фабрике закончена, мы посмотрели все этапы создания плитки, посмотрели производство отельных элементов, познакомились с техниками нанесения рисунка" - закончила свой рассказ технолог производства.
Нам очень понравилось! во время экскурсии мы узнали много тонкостей, которые важны в работе.
За организацию большое спасибо сотрудникам Kerama Marazzi.
Это вторая часть экскурсии, обязательно прочитайте про завод сантехники Kerama Marazzi
Нам очень понравилось! во время экскурсии мы узнали много тонкостей, которые важны в работе.
За организацию большое спасибо сотрудникам Kerama Marazzi.
Это вторая часть экскурсии, обязательно прочитайте про завод сантехники Kerama Marazzi